铜箔作为新能源与电子产业的核心材料,其表面质量直接影响锂电池与PCB性能。面对传统人工检测0.6%漏检率带来的年超20亿元损失,无锡光合智能装备通过自主研发的瑕疵在线检测系统,以“CCD+AI视觉”技术破解行业难题。该系统采用16K线性CCD阵列、深度卷积神经网络(DCNN)及3D数字孪生技术,实现10μm级瑕疵检测与99.98%检出率,助力客户单线年省超500万元。文章进一步展望量子点光谱、X射线能谱联用等前沿技术,揭示智能检测从“质量控制”向“预测性生产”的变革路径。
一、产业痛点:铜箔表面检测的世纪难题
随着新能源汽车与5G通信产业的爆发式增长,铜箔作为锂电池负极集流体和高端PCB的核心材料,其质量直接决定终端产品性能。2023年全球铜箔需求量突破120万吨,但表面瑕疵检测仍是行业难题。数据显示,0.1mm级划痕或氧化点即可导致电池自放电率上升30%,而传统人工检测的0.6%漏检率每年造成超20亿元经济损失。铜箔生产向3μm极薄化演进,对检测精度、效率和稳定性提出更高要求。
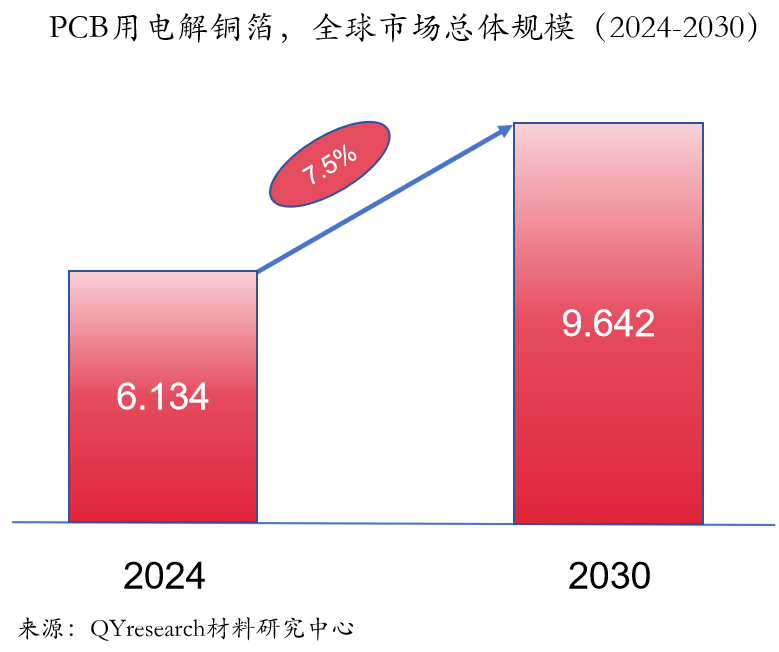
二、技术突破:CCD视觉系统与AI的融合创新
1. CCD技术原理与行业价值
CCD(电荷耦合器件)表面检测技术通过高分辨率相机对铜箔表面进行非接触式扫描,结合图像处理算法精准识别划痕、凹坑、杂质等瑕疵,具有速度快、精度高、稳定性强等优势,成为铜箔质量控制的基石。
2. 无锡光合的“三线协同”创新架构
公司自主研发的瑕疵在线检测系统,以AI视觉为核心构建多维技术矩阵:
高速成像层:16K线性CCD阵列实现10μm/pixel分辨率,检测速度达35m/min;
智能算法层:基于深度卷积神经网络(DCNN)的缺陷分类模型,支持23类瑕疵特征自学习;
数字孪生层:突破传统2D成像局限,实现表面凹陷、凸起等立体形貌的精准捕捉,使普通工业相机具备类2.5D视觉的纹理解析能力。
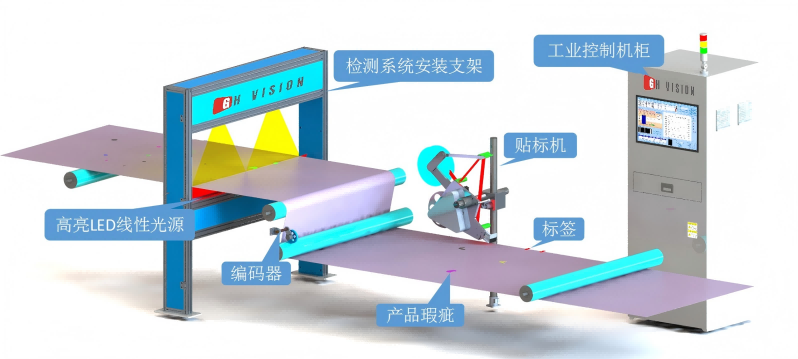
三、落地实践:从技术到效益的全链升级
在头部锂电客户的4.5μm超薄铜箔产线中,光合智能瑕疵在线检测系统实现:
检测效能跃迁:缺陷检出率提升至99.98%(较传统提升4个数量级),漏检率趋近于零;
生产稳定性优化:月均故障停机时间由36小时降至2.4小时,设备综合效率(OEE)提升25%;
质量成本重构:MES系统联动实现全流程数据追溯,单线年度质量成本节省超500万元。
案例实证:某客户引入系统后,瑕疵检出率提升30%,良品率突破99.5%,年经济损失减少超2000万元。
四、创新延伸:技术生态与未来布局
无锡光合以AI视觉为支点,构建开放式技术生态:
方案端:基于模块化架构提供柔性检测方案,可根据产线速度、材料特性及缺陷标准定制检测方案与系统,支持16K/8K/4K线阵相机自由组合。
边缘端:部署轻量化AI推理引擎,算力功耗降低40%;
云端:搭建材料缺陷数据库,并持续更新,收录超200万条缺陷特征。
五、行业展望:从检测到预测的智造变革
随着铜箔极薄化趋势加速,无锡光合技术总监指出:“质量大数据平台将实现工艺参数与缺陷图谱的智能关联,推动生产从‘事后检测’转向‘预测性调控’。”未来,智能检测技术不仅保障品质,更将反向赋能工艺优化,引领铜箔制造进入“零缺陷”新纪元。
六、结语
CCD表面检测技术正重塑铜箔产业的质量标准。无锡光合智能装备通过“AI+视觉”的创新融合,为行业提供从精密检测到数据驱动的全链解决方案,成为智造升级的核心引擎。在技术迭代与生态协同的双重驱动下,铜箔产业的品质天花板将持续突破。