一、行业爆发下的质量挑战
随着汽车后市场消费升级,TPU车衣膜凭借其卓越的耐刮擦、抗黄变和自修复性能,成为高端汽车保护的标配。数据显示,2024年全球市场规模已突破17.5亿美元,中国持续贡献超36%的产能,长三角地区仍占据国内产量的半壁江山。然而,在行业高速发展的背后,传统生产模式正面临严峻挑战:
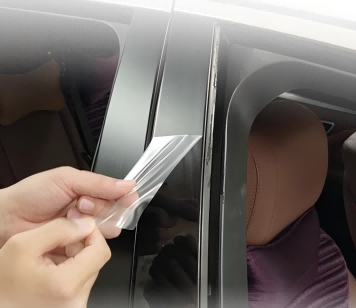
1. 人眼质检的极限困境
产线速度达20米/分钟,质检员需在0.3秒内完成1平方米区域的缺陷识别,实际漏检率高达18%,每年因表面瑕疵导致的客户投诉损失超6亿元。
2. 复杂工艺的精度失控
从涂布、压延到分切,TPU膜生产涉及十余项关键参数控制。传统方法难以实时监测厚度波动(±0.02mm公差)、微米级划痕(<10μm)等隐形缺陷,导致产品抗冲击性下降30%,使用寿命缩短40%。
3. 高反光环境的检测盲区
TPU材料表面反光率超85%,普通工业相机在强光干扰下误报率达25%,企业不得不投入额外40%的人力进行复检。
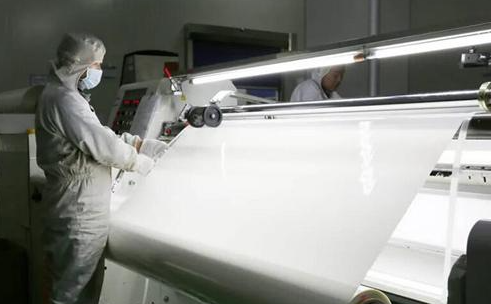
二、技术破局:视觉检测重塑行业质量标准
在智能制造浪潮下,无锡光合智能装备有限公司凭借自主研发的表面瑕疵检测系统,为TPU车衣膜行业提供了全流程质量管控解决方案,攻克了三大技术壁垒:
1. 高精度成像:让隐形缺陷无处遁形
多光谱融合技术:集成900-1700nm短波红外与可见光成像,精准捕捉微气泡(0.05mm³)、晶点杂质等传统手段难以识别的缺陷,检出率达99.2%。
动态偏振矩阵:通过16组可编程偏振片阵列,实时调节光路角度,将高反光场景下的划痕识别准确率提升至93%,误报率降至3%以下。
2. 智能化闭环:从检测到工艺优化
光合智能的表面瑕疵检测系统不仅可以实现高速在线检测,还将平台与生产设备实时联动:
涂布环节:自动调节温度(±0.5℃)与压力(±0.1MPa),减少涂层不均问题
压延阶段:动态控制辊距(±1μm),降低流痕缺陷发生率
分切工序:智能调整张力(±0.5N),避免边缘毛刺产生
3. 数据驱动:构建行业质量知识库
依托百万级缺陷样本数据库(含17类主缺陷、83个子类型),系统搭载的YOLOv7改进模型可实现:隐形划痕检出率91.3%,较传统算法提升31%;在线自主学习功能,每日更新3000+新样本,适应新型缺陷演化
三、无锡光合智能:本土智造的技术标杆
作为长三角高端装备制造的代表企业,无锡光合智能装备有限公司深耕机器视觉领域十余年,其检测系统已形成核心优势:
1. 自适应降噪+OPC UA深度集成
动态深度学习算法:创新采用自适应降噪技术,在高速产线及400℃高温环境下仍保持稳定检测性能;智能决策系统:通过OPC UA协议实现与MES/ERP系统深度集成,自动生成12类质量分析报表,追溯效率提升60%。
2. 工业级可靠性设计
通过IP67防护认证,支持7×24小时连续运行,平均无故障时间超5万小时,适配TPU膜工厂的高温高湿环境。
3. 成本效益革命
设备价格较进口品牌低40%,维护成本减少60%,帮助客户平均11个月收回投资(行业平均22个月)。
标杆案例:某上市公司改造实录
改造前:2.2米宽幅产线月均质量损失320万元,客诉率行业垫底
部署方案:3台系统
成效对比:良品率从84.3%跃升至96.8%;月均质量损失锐减85%,年节省成本超3000万元;ROI回收周期仅9个月,创行业新纪录
中国技术将定义全球标准在TPU车衣膜这个千亿级赛道中,视觉检测技术已成为质量竞争的核心战场。无锡光合智能装备有限公司通过持续创新,不仅解决了行业痛点,更推动中国制造从“代工生产”向“质量输出”跨越。其表面瑕疵检测系统已在长三角50余条产线成功应用,助力客户实现质量溢价20%-35%。
未来,随着5G+工业互联网的深度融合,光合智能将继续引领行业向智能制造闭环演进,让每一卷TPU车衣膜都成为“中国质造”的金色名片。